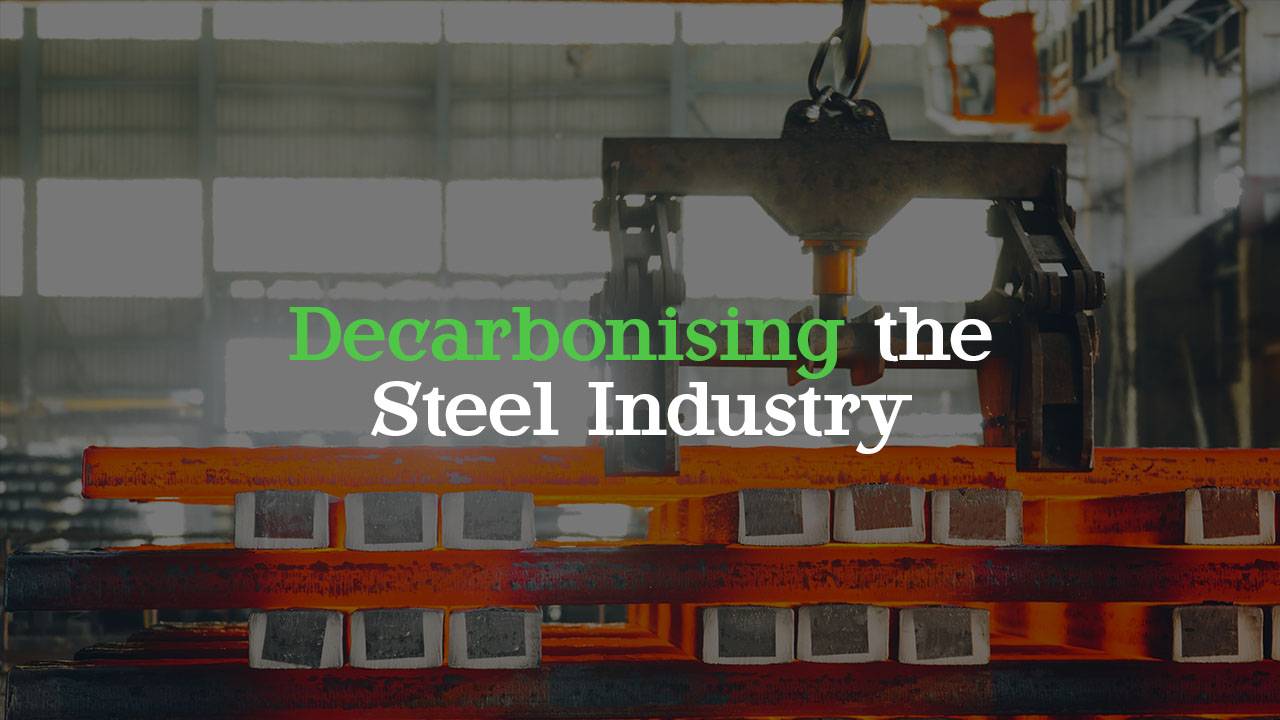
Climate change is not just about warmer temperatures; it’s about profound shifts in our planet’s balance. While natural factors like solar cycles influenced climate in the past, human activities since the 1800s, particularly burning fossil fuels like coal, oil, and gas, have become the primary driver. These actions have wrapped the Earth in a layer of greenhouse gases, trapping heat and raising the planet’s temperature by 1.1°C since the late 1800s.
The impacts are far-reaching: rising sea levels, intense droughts, floods, severe storms, and biodiversity loss. These interconnected effects ripple across the globe, affecting ecosystems, livelihoods, and economies.
Steel’s Role in Climate Change
Steel is the backbone of modern development, but its production is a major contributor to carbon emissions. India’s steel industry, which has grown from 22 million tonnes in the early 1990s to 120 million tonnes today, is largely reliant on coal.
The Direct Reduced Iron (DRI) process, dominant in India, emits 3.0–3.1 tons of CO2 per ton of steel, making it a high-emission method. In contrast, using Electric Arc Furnaces (EAFs) with scrap emits only 0.7 tons of CO2 per ton, significantly reducing the carbon footprint. However, India faces two critical challenges:
- A shortage of scrap for steel production.
- Limited availability of natural gas as an alternative energy source.
These constraints force Indian companies to rely heavily on coal, further increasing emissions.
Emission Sources:
- Process emissions during raw material transformation.
- Combustion of fossil fuels like coal and natural gas.
- Indirect emissions from electricity usage.
Key processes contributing to emissions:
- Coke Production: Heating coal to produce coke contributes ~20% of CO2 emissions.
- Iron Blast Furnaces: Carbon reacts with iron oxide to produce molten iron, releasing CO2.
- Direct Reduced Iron (DRI): Reduction of iron ore using coal or natural gas produces CO2.
- Crude Steel Production: Basic Oxygen Furnace (BOF) and Electric Arc Furnace (EAF) together contribute ~15% of CO2 emissions.
- Rolling and Finishing: Heating fuels and electricity add ~15–20% of emissions.
Conventional Steel Production Routes
Steel production relies on three primary routes: Blast Furnace – Basic Oxygen Furnace (BF-BOF), Electric Arc Furnace (EAF), and Direct Reduced Iron – Electric Arc Furnace (DRI-EAF), each varying in emissions and raw materials. These methods are foundational but require innovation for greener, more sustainable steelmaking.
BF-BOF (Blast Furnace – Basic Oxygen Furnace):
- Process: This is the traditional method of steelmaking, where iron ore is reduced to molten iron in a blast furnace using metallurgical coal. The molten iron is then refined in the Basic Oxygen Furnace to produce steel.
- Emission Intensity: 4.3 CO2/tCS (tons of CO2 per ton of crude steel produced).
- Raw Materials: Primarily relies on metallurgical coal as the reducing agent and iron ore as the input material.
EAF (Electric Arc Furnace):
- Process: Steel is produced using scrap steel as the primary input. This method primarily relies on electricity for the heating and melting process, making it a lower-carbon alternative.
- Emission Intensity: 0.3 CO2/tCS.
- Raw Materials: Scrap steel, which is recycled material, significantly reduces the carbon footprint of the process.
DRI-EAF (Direct Reduced Iron – Electric Arc Furnace):
- Process: Iron ore is reduced to sponge iron using natural gas or coal (in India, it’s coal-based), followed by melting in an Electric Arc Furnace to produce steel.
- Emission Intensity: 1.4 CO2/tCS.
- Raw Materials: Uses iron ore for the reduction process, coupled with the use of EAF.
Emission Insights
- BF-BOF has the highest emissions due to its dependence on metallurgical coal as a reducing agent.
- EAF, leveraging scrap steel, has the lowest emissions among these routes, highlighting the importance of scrap utilization for decarbonization.
- DRI-EAF serves as a middle ground, with emissions significantly lower than BF-BOF but higher than EAF, primarily due to the use of coal or natural gas in the reduction process.
Regulations around Steel Industry
The iron and steel industry in India operates under stringent environmental regulations outlined by the Environment Protection Act (EPA) and accompanying rules enacted by the Ministry of Environment, Forest, and Climate Change (MoEF&CC). Before establishing new plants or expanding existing ones, companies must obtain statutory clearances and adhere to pollution control standards for air, water, noise, and solid waste, as monitored by Central and State Pollution Control Boards. Additionally, the Ministry of Steel facilitates the formulation and revision of norms to support compliance.
Energy Management
Indian steel plants consume 6-6.5 Giga Calories of energy per tonne of crude steel, significantly higher than the 4.5-5.0 Giga Calories consumed by steel plants abroad. This is due to outdated technologies, older operating practices, and lower-quality raw materials, such as high ash coal and high alumina iron ore. However, energy consumption is gradually decreasing through:
- Technological upgrades.
- Waste heat utilization.
- Improved raw material quality.
The government, through various initiatives, is driving improvements in energy efficiency and environmental sustainability in steel plants.
Decarbonisation Efforts in the Steel Industry
1. Corporate Responsibility for Environment Protection (CREP)
An initiative by the MoEF&CC, CREP involves steel plants in reducing pollution, energy and water consumption, and managing solid and hazardous waste. Measures include waste minimization, clean technology adoption, and in-plant process control. The Ministry of Steel works with a National Task Force to implement CREP actions.
2. National Action Plan on Climate Change (NAPCC)
Launched in 2008, NAPCC addresses climate challenges through eight missions, including the National Mission for Enhanced Energy Efficiency (NMEEE). The Perform, Achieve & Trade (PAT) scheme under NMEEE incentivizes energy savings, allowing steel units exceeding their targets to trade energy-saving certificates. The scheme currently covers 163 iron and steel units, which have collectively achieved significant reductions in energy consumption and emissions.
3. Energy Efficiency in SME Steel Plants
Projects like the UNDP-GEF-MoS initiative (2004-2013) and the UNDP-MoS-AusAID initiative (2013-2016) introduced energy-efficient technologies in steel re-rolling mills and induction furnaces. These efforts led to 20-30% reductions in specific energy consumption and annual reductions of ~400,000 tonnes of CO2.
4. NEDO Model Projects
The Government of Japan, through its Green Aid Plan, funds energy-efficient projects in India’s steel sector. Notable examples include:
- BF Stove Waste Heat Recovery (Tata Steel).
- Coke Dry Quenching (Tata Steel).
- Sinter Cooler Waste Heat Recovery (RINL).
5. Iron & Steel Slag Utilization
Integrated steel plants produce substantial waste, including blast furnace (BF) slag and steel melting shop (SMS) slag. BF slag is almost entirely reused, primarily in cement making. However, SMS slag utilization remains limited due to its phosphorus and lime content. Ongoing research aims to expand its use in construction, soil conditioning, and road-making.
R&D projects are underway to develop design guidelines for slag use in road construction and cementitious materials, contributing to a circular economy.
Progress on Nationally Determined Contributions (NDCs)
India’s steel industry is aligned with the nation’s climate goals, committing to reduce emissions intensity by 33-35% by 2030 from 2005 levels. Specific achievements include:
- Reducing CO2 emissions intensity from 3.1 tonnes/tonne of crude steel (2005) to 2.5 tonnes/tonne (2020).
- Implementing clean technologies such as coke dry quenching, waste heat recovery, and energy-efficient rolling processes.
Key Challenges
- Structural Dependence on Coal: India’s steel industry predominantly relies on coal-based methods such as blast furnaces, which are highly carbon-intensive. The emission intensity from these processes stands at 2.54 tCO₂ per tonne, significantly above the global average of 1.91 tCO₂.The limited availability of high-quality scrap metal hampers the transition to electric arc furnaces (EAFs), which are less carbon-intensive but require substantial amounts of scrap as feedstock. Additionally, high costs associated with natural gas limit its use as an alternative fuel source in steel production.
- Definition of Green Steel: There is currently no universally accepted definition of “green steel,” leading to confusion in standards and certifications. India must navigate this ambiguity while striving for emission intensity targets that align with its national climate agenda. Balancing gradual decarbonisation efforts with economic growth presents a challenge; industries need clear guidelines on what constitutes green practices.
- Carbon Emissions Monitoring: Current emissions reporting primarily focuses on Scope 1 (direct emissions from owned or controlled sources) and Scope 2 (indirect emissions from purchased electricity). However, comprehensive data on Scope 3 emissions (indirect emissions from the value chain) is lacking due to difficulties in data collection and verification. As India’s carbon market evolves, full tracking of emissions will become mandatory, necessitating robust monitoring, reporting, and verification protocols across all scopes.
- High Costs of Decarbonisation Technologies: Technologies such as Carbon Capture, Utilisation, and Storage (CCUS) are essential for reducing emissions but remain prohibitively expensive due to low concentrations of CO₂ in industrial emissions. Developing cost-effective solutions for carbon capture that can be integrated into existing production processes is crucial but presents significant technical challenges.
- Stimulating Demand for Green Steel: The successful adoption of green steel hinges on creating market demand through supportive policies like a Green Public Procurement Policy that prioritizes low-carbon products in public sector purchases. Certification systems that track and verify reductions in emissions associated with green steel production are still underdeveloped, making it difficult for consumers and businesses to identify truly sustainable products.
Opportunities for Transformation in the Steel Sector
- Technological Innovations: Green hydrogen can serve as a clean reducing agent that replaces coal in iron ore reduction processes. This innovation could drastically cut emissions associated with traditional methods. Deploying renewable electricity sources within steel plants can help decarbonise energy consumption significantly while also providing cost savings over time.
- Carbon Capture and Energy Efficiency: Integrating CCUS technologies into existing production processes can facilitate deeper decarbonisation by capturing CO₂ before it enters the atmosphere. The success demonstrated by the PAT scheme indicates potential for further energy savings through enhanced operational efficiencies and technological upgrades across facilities.
- Renewable Energy Integration: With projections indicating that electricity demand will double by 2030, there is an urgent need for integrating renewable sources into the grid. This shift not only supports decarbonisation goals but also enhances energy security for industrial operations.
- Global Leadership Potential: By addressing these challenges effectively, India has the opportunity to position itself as a global leader in green steel production by 2070. This leadership role could involve exporting low-carbon technologies and practices internationally while setting standards for sustainable manufacturing.
Conclusion
Decarbonizing India’s steel industry is vital for achieving national climate goals and staying competitive in a global market that values sustainability. This requires clear policies defining green steel, investments in green hydrogen, renewable energy, and carbon capture, as well as robust emissions monitoring to ensure accountability and drive greener practices.
Having met its 2020 emissions targets, the industry is on track for 2030 goals, balancing growth with environmental responsibility. With continued innovation and collaboration between government and industry, India’s steel sector can lead in sustainable, low-carbon production and contribute to a greener global economy by 2070.