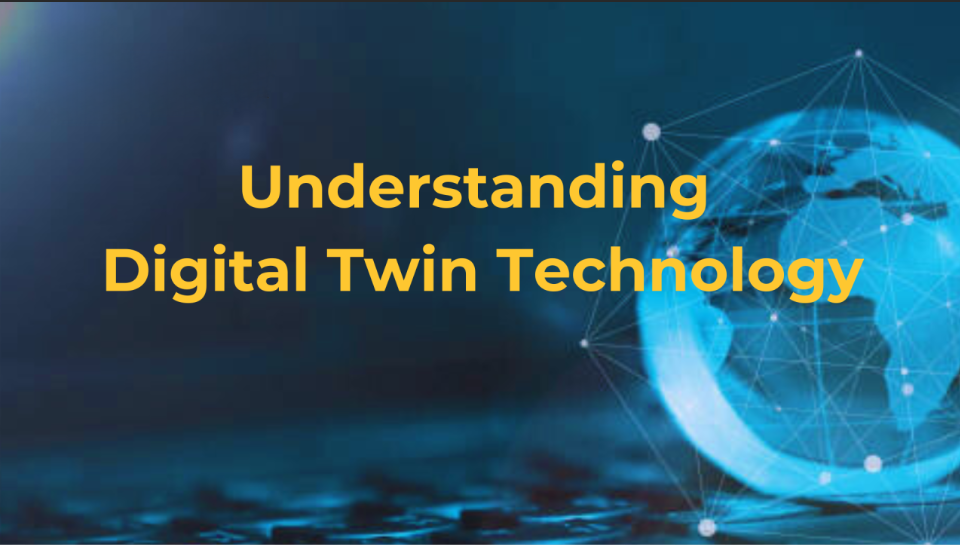
The origins of digital twin technology in India can be linked to the global progress made in Industry 4.0, which prioritizes automation, data sharing, and intelligent manufacturing. Although the concept gained international attention through organizations like NASA in the aerospace sector, Indian companies have quickly adopted this technology to boost operational efficiency and drive innovation.
In recent years, many Indian startups and established businesses have started to create digital twin solutions specifically designed for a range of industries. For example, one company is concentrating on building solar power infrastructure by providing analytics tools that enhance performance forecasting and power prediction. Likewise, another company is developing digital twins for power distribution utilities to improve service delivery and customer interaction. The Indian government’s projects, such as the Sangam Digital Twin initiative, aim to merge digital twin technology with AI and IoT to enhance infrastructure planning and management in urban areas.
Building on the growing adoption of digital twin technology, it can also be seen as a critical tool in addressing India’s future energy needs. With the country ranking third globally in installed renewable energy capacity and power consumption expected to reach 708 GW by 2047, digital twins offer innovative solutions to address these challenges and drive sustainable growth.
What is Digital Twin?
A digital twin is a dynamic, real-time replica of a physical product, system, or process that is created to analyze and predict the efficiency of the real version. It brings together data from various sources to provide a comprehensive view of the system and its behaviors. Essentially, a digital twin is like a smartwatch for things like solar panels or wind turbines. Just like a smartwatch tracks your heart rate, steps, and sleep, a digital twin tracks how something works, finds problems early and even predicts what might go wrong later.
This technology works by creating a virtual model, or simulation, of a product or production system before any physical versions are built. This allows designers and engineers to test and refine their ideas digitally, saving time and money that would otherwise be spent on creating physical prototypes.
For example, instead of building a real asset, a virtual version can be developed and optimized on a computer to ensure it works perfectly. The real power of this technology lies in the precise data it combines. By carefully analyzing and refining every small detail of the design or process, digital twins can make systems more efficient and improve the overall workflow. This not only provides a clear view of many possible setups but also ensures that the final version is as effective and cost-efficient as possible.
Key Benefits of Digital Twin:
- Real-Time Monitoring: Operators can detect faults and inefficiencies early, ensuring uninterrupted power supply.
- Predictive Maintenance: Anticipates equipment degradation, allowing for timely repairs and minimizing downtime.
- Operational Optimization: Simulates scenarios to maximize energy production and resource efficiency.
The Future of Digital Twin in Renewable Energy
As global energy demand continues to rise, the role of digital twins in the renewable energy sector will become increasingly vital:
- Scaling Renewables: Digital twins facilitate the optimization of large-scale renewable projects by providing insights into operational efficiencies.
- Improving Grid Reliability: Virtual models enhance energy distribution management and fault detection across power grids.
- Driving Innovation: The integration of digital twins with artificial intelligence (AI) and the Internet of Things (IoT) will unlock new levels of efficiency and innovation in renewable energy management.
For example, digital twins can simulate the performance of solar panels under different weather conditions, helping optimize energy output and reduce downtime. Or, they could monitor wind turbines in real-time, identifying potential issues before they lead to costly breakdowns.
Virtual Prototype vs Digital Twin
A virtual prototype is a static model, primarily used during the design phase to test and refine ideas before physical development. In contrast, a digital twin is dynamic, intelligent, and evolves alongside the real-world system it represents, offering real-time insights, predictive capabilities, and lifecycle support.
Virtual Prototype: One designs a solar panel and tests it virtually to see if it can handle heavy rain or extreme heat. Once tested, the virtual model becomes less useful because the real solar panel is built.
Digital Twin: After the solar panel is built and installed, a digital twin continues to work. It updates based on real-time data, shows how well the panel is performing every day, predicts when it might need cleaning or repairs, and even runs simulations to suggest better panel angles for more sunlight. This technology transforms decision-making processes across various renewable energy projects by:
- Evaluating Design Alternatives: Digital twins allow stakeholders to assess different design strategies, such as storage capacities and configurations, ensuring that the most efficient options are selected.
- AI Optimization: Unlike a virtual prototype, which is limited to what you program it to do, a digital twin uses AI and machine learning to analyze data. It can suggest ways to improve efficiency, predict when parts will fail, or even recommend the best design alternatives based on real-world feedback.
- Performance Simulation: They simulate and compare the performance of various components under diverse conditions, providing crucial insights that inform operational adjustments.
For example, one can test how a solar panel will perform under cloudy weather, extreme heat, or different cleaning schedules—even while the actual panel is in use.
How Digital Twin Technology Works
The effectiveness of digital twin technology hinges on several key processes:
- Data Collection: Sensors embedded in physical assets gather real-time information on parameters such as temperature, pressure, and vibrations.
- Virtual Modeling: This data is used to create a dynamic digital replica that evolves as new information is collected.
- Simulation and Analysis: The digital twin simulates various operational scenarios to predict performance outcomes and identify inefficiencies.
- Actionable Insights: Operators receive recommendations for improving performance, extending asset lifespans, and reducing operational costs based on the analysis.
Key Use Cases of Digital Twin in Renewable Energy
- Power Firmness: Maintaining a balance between intermittent renewable energy sources and storage solutions is vital for consistent power output. Digital twins facilitate comparisons between low-cost power sources and their corresponding energy storage needs.
- Load Factor Management: Digital twins offer valuable insights into the degradation of key components and its impact on operational costs.
- Process Design Integration: For large-scale industrial processes reliant on renewable energy, digital twins help optimize power-to-molecule systems by balancing capital expenditures on renewable sources with operational uptime.
- Subcomponent Selection: The choice of Balance of Plant (BoP) components significantly affects both capital and operational expenditures. Digital twins assist developers in deciding between fewer larger components or smaller redundant modules.
- Product Storage Optimization: Effective storage solutions are critical in renewable energy projects. Digital twins aid in assessing trade-offs between smaller, riskier storage options and larger buffers.
Applications of Digital Twin Technology in Renewable Energy
1. Solar Farm Monitoring
Managing large solar farms can be challenging due to the sheer number of panels involved. Digital twin technology plays a pivotal role in ensuring optimal performance:
- Real-Time Asset Monitoring: Digital twins continuously monitor each panel’s performance, detecting faults early and ensuring an uninterrupted power supply.
- Predictive Maintenance: By analyzing historical data and current performance metrics, digital twins can anticipate panel degradation and schedule timely repairs.
- Performance Optimization: Simulations allow operators to adjust panel angles for maximum sunlight absorption, significantly reducing operational costs.
2. Wind Farm Performance and Maintenance
Wind turbines are subject to constant environmental stressors that can lead to structural damage over time. Digital twin technology enhances wind farm management through:
- Structural Monitoring: Digital twins track vibrations and other stress factors on turbines, preventing damage from harsh weather conditions.
- Predictive Analysis: By analyzing wear patterns, digital twins can forecast equipment failures, allowing for timely interventions that reduce downtime.
- Operational Optimization: Adjusting turbine angles based on real-time wind patterns maximizes energy generation efficiency.
3. Hydropower System Maintenance
Hydropower plants are critical components of the renewable energy mix but face unique operational challenges due to aging infrastructure:
- Automated Monitoring: Digital twins enable real-time tracking of turbine and generator conditions, ensuring optimal performance.
- Data-Driven Maintenance: By identifying potential issues before they escalate into significant problems, digital twins help maintain system efficiency.
- Enhanced Data Accuracy: Utilizing drones and advanced monitoring tools improves precision in tracking asset conditions.
Conclusion
Digital Twin’s application across solar, wind, and hydropower sectors demonstrate its immense potential to enhance efficiency, reduce costs, and support sustainable energy goals. Stakeholders across the renewable energy sector must embrace digital twins as essential tools for navigating the complexities of modern energy demands.