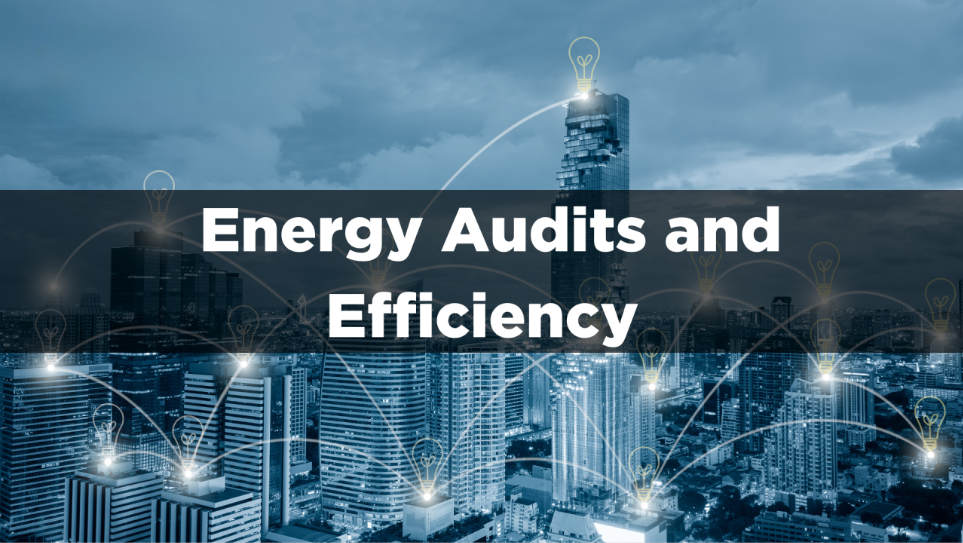
Energy Audits and Efficiency
Energy audits are vital for organizations aiming to enhance energy efficiency, reduce costs, and minimize their environmental footprint. This guide provides a detailed framework for conducting comprehensive energy audits, identifying inefficiencies, and implementing effective energy-saving measures.
For further details or assistance with your energy audit, reach out to us at contact@btgreenenergy.com and discuss this over a free consultation call.
The Importance of Energy Audits
Conducting energy audits is crucial for several reasons:
- Cost Reduction: Energy costs can constitute a significant portion of operational expenses. By identifying and addressing inefficiencies, companies can substantially reduce their energy bills. For example, energy audits in industrial facilities have been shown to reduce energy costs by up to 30%.
- Regulatory Compliance: The Indian government has implemented various regulations and schemes to promote energy efficiency, such as the Perform, Achieve, and Trade (PAT) scheme. Compliance with these regulations not only avoids penalties but also positions companies to benefit from incentives.
- Environmental Impact: Reducing energy consumption lowers greenhouse gas (GHG) emissions, helping companies contribute to India’s climate goals. According to the Ministry of Environment, Forest and Climate Change, enhancing energy efficiency could help reduce India’s CO2 emissions by up to 1 billion tons by 2030.
Conducting Comprehensive Energy Audits
Defining the Scope and Objectives
The first step in a comprehensive energy audit is to clearly define its scope and objectives. This process ensures that the audit remains focused and delivers actionable outcomes.
- Goals: Establish specific, measurable goals, such as reducing energy consumption by 20% over two years, improving energy efficiency, or complying with regulatory requirements.
- Focus Areas: Identify high-energy-use areas such as HVAC systems, lighting, and industrial processes. Consider areas with known inefficiencies or previous audit findings.
Setting clear objectives allows organizations to tailor their audit efforts effectively, ensuring that resources are allocated to areas with the highest potential impact.
Data Collection and Analysis
Accurate data collection is the backbone of a successful energy audit. It involves gathering historical energy usage data, operational data, and building information.
Data Collection:
- Energy Consumption: Collect at least 12-24 months of utility bills to understand seasonal variations. Use sub-metering systems for detailed data from specific equipment or areas.
- Operational Data: Record operational schedules, equipment specifications, and maintenance logs. Analyze production data to correlate energy usage with operational output.
- Building Information: Document architectural features, insulation levels, and HVAC system details. Utilize Building Information Modeling (BIM) for detailed energy use models.
Data Analysis:
- Regression Analysis: Identify patterns and correlations in energy consumption.
- Energy Modeling Software: Use tools like RETScreen and DesignBuilder to simulate scenarios and predict the impact of energy-saving measures.
The analysis phase provides a clear understanding of where energy is consumed and highlights areas of inefficiency.
On-Site Inspections
On-site inspections are crucial for identifying real-world inefficiencies. These inspections should be thorough and systematic.
- Equipment Performance: Evaluate major energy-consuming equipment such as boilers, chillers, and lighting systems. Use infrared thermography to detect heat losses and inefficiencies in HVAC systems.
- Operational Practices: Observe employee behavior and operational practices impacting energy consumption. Conduct interviews with facility managers and staff to gain insights.
- Thermal Imaging and Blower Door Tests: Identify areas of heat loss, poor insulation, and inefficient HVAC operations. Measure the airtightness of buildings to identify leaks.
Detailed on-site inspections uncover inefficiencies that data alone might not reveal, providing a comprehensive picture of energy usage.
Identifying Energy Inefficiencies and Opportunities for Improvement
Identifying prevalent inefficiencies is essential for prioritizing energy-saving measures.
Lighting Systems:
- Inefficiency: Older fluorescent and incandescent lighting systems consume more energy than modern LED systems.
- Improvement Opportunity: Retrofit lighting with LED fixtures, install motion sensors, and optimize the use of natural light.
The Ministry of Power’s UJALA scheme reports that LED retrofits have led to a reduction of over 38 million tons of CO2 annually.
HVAC Systems:
- Inefficiency: Outdated or poorly maintained HVAC systems often lead to excessive energy consumption.
- Improvement Opportunity:Upgrade to high-efficiency HVAC units, implement regular maintenance, and use programmable thermostats.
Studies suggest that efficient HVAC systems can reduce energy usage by 20-30%.
Insulation:
- Inefficiency: Poor insulation leads to heat loss in winter and heat gain in summer, increasing energy usage.
- Improvement Opportunity: Enhance insulation in walls, roofs, and windows to reduce heating and cooling demands.
Enhancing insulation can reduce heating and cooling costs by 15-25%.
Process Equipment:
- Inefficiency: Overloaded or under-maintained machinery in manufacturing processes can lead to significant energy waste.
- Improvement Opportunity: Upgrade to high-efficiency motors and drives, optimize process controls, and implement preventive maintenance programs.
Research estimates that improving motor efficiency can save up to 30% of energy used in industrial processes.
Energy Modeling and Benchmarking
Energy modeling and benchmarking help identify areas with the highest potential for improvement.
Energy Modeling:
- Purpose: Simulate energy consumption scenarios to evaluate the impact of various energy-saving measures.
- Tools: Utilize software like RETScreen, DesignBuilder, and Integrated Environmental Solutions (IES) for detailed energy simulations.
Energy modeling can predict energy savings with an accuracy of ±10%, providing a reliable basis for decision-making.
Benchmarking:
- Purpose: Compare your energy usage with industry standards and best practices to identify inefficiencies.
- Approach: Use benchmarks like Energy Use Intensity (EUI) to gauge performance.
According to the BEE’s Perform Achieve and Trade (PAT) scheme, industries that benchmark their energy use can achieve significant efficiency improvements.
Tracking Progress and Continuous Improvement
Regular monitoring and continuous improvement are essential for sustaining energy savings. Implement energy management systems (EMS) to monitor and control energy usage in real-time, which helps identify and rectify inefficiencies promptly.
Establish key performance indicators (KPIs) such as Energy Use Intensity (EUI) and cost per unit of production. KPIs provide measurable targets for continuous improvement. Conduct periodic energy audits to identify new opportunities and track the effectiveness of implemented measures.
Conclusion
Conducting comprehensive energy audits, identifying inefficiencies, and implementing targeted energy-saving measures are crucial steps for sustainability professionals aiming to enhance energy efficiency and reduce operational costs. By leveraging data-driven insights and adopting a systematic approach, C&I companies in India can achieve substantial energy savings and contribute to a more sustainable future. Regular monitoring and continuous improvement ensure that energy efficiency becomes an integral part of business operations, driving long-term success.Report this article
Post a comment Cancel reply
Related Posts
How Energy Audits Can Boost Your ESG Score: A Smart Strategy for Sustainable Growth
How Energy Audits Can Boost Your ESG Score: A Smart Strategy for Sustainable Growth In…
How Eco Check Empowers Businesses To Reduce Emissions
How Eco Check Empowers Businesses To Reduce Emissions In today’s business landscape, climate responsibility is…
New SEBI ESG Debt Guidelines Raise the Bar—But Do Mid-Sized Companies Have a Ladder?
New SEBI ESG Debt Guidelines Raise the Bar—But Do Mid-Sized Companies Have a Ladder? SEBI’s…
Ecopurus Certification: Why It Matters And How To Achieve It
As people talk more about climate change and protecting the environment, businesses are expected to…